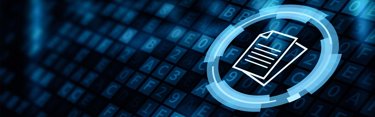
Resources
Filter
Filter
Sort
1 - 12 of 15 results
Here to achieve, validate and demonstrate compliance
Our expert consultants are available to ensure compliant and effective processes for asset design, build, maintenance, and operation.
Contact our experts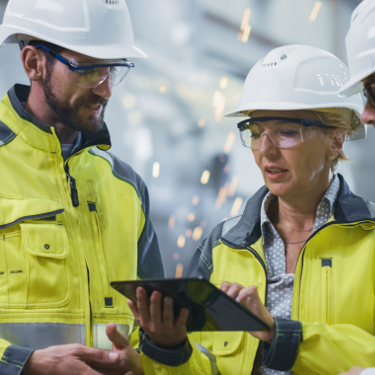